Level Measurement in industries is very important and critical. In this article, you can find out all about industrial level measurement with a free eBook.
Industrial Level Measurements
Why Measure level?
- To keep track of the amount of material available for a process in inventory
- To monitor the amount of material that is bought & sold in terms of volume or weight
- To attain maximized storage tank capacity
- To prevent the unnecessary expense of purchasing additional vessels
- To prevent spillage in open vessels
- To prevent overpressure conditions in closed vessels that may result in rupture
- To maintain product quality and consistent supply in a process
Level terminology | Parameters
- Interface
- Density
- Mass
- Volume
- Level
- Interface
Interface measurement finds the boundary between two liquids stored in the same tank in which each liquid has a different density.
- Density
Density is a measure of the mass per volume
Example: kg/m3
Specific Gravity is a ratio of the density of a fluid to the density of water, thus,
- SG = Density of Fluide / Density of Water
- The density of fluid = density of water * SG
- Mass = Density / Volume
- Volume
1. Volume only correlates directly to level when:
- The tank is an upright cylinder
- Density is constant
- The temperature is constant
- There is no change in tank wall position after filling
2. Volume measurements are in units such as
- gallons, liters, barrels…
3. Level measurements are in units such as
- inches, feet, millimeters, centimeters, meters…
4. The correlation of volume to level varies with the geometry of the tank and may be expressed in terms such as
- gal/inch, liters/meter, barrels/inch…
Industrial Applications
- Viscous liquids
- Abrasive liquids
- Steam, Vapor, Dust
- Density Changes
- High Vacuum
- Viscous or sticky fluids
- Foaming
- Corrosive Process
- Extreme Temperatures
Measurement Characteristics
Bottom-Up vs. Top-Down Measurement
1. Top-Down Measurement
•Poses less potential for leakage
•devices installed or removed without emptying the tank
e.g., dipstick, radar
2. Bottom-Up Measurement
•Typically contacts the process fluid
e.g., pressure transmitter, weight scale
3. Inferred vs. Direct Measurement
•An Inferred measurement is derived from another measurement
Ex: pressure transmitter
Head Pressure = Liquid Density * Gravity Acceleration (g) * Liquid Hight
•Stability of variables is critical to get a good inferred measurement.
•If variables are not stable, compensation needs to be made.
•A Direct measurement looks only at the desired variable
ex: floats, dipsticks, Radar, Ultrasonic
Where to use Continuous and Point measurement?
1. Point Level Measurement
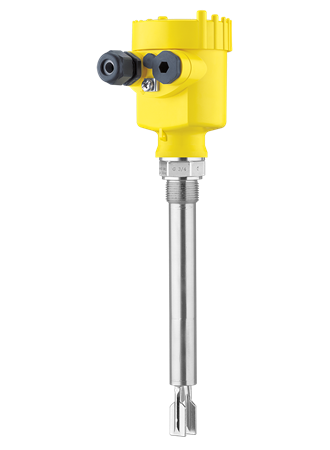
- Has the level reached this point?
- High or Low-Level Detection
- Often used for alarm control
- May start or stop pumps
- May open or close valves
2. Continuous Level Measurement

•Constant detection of product height
•Concerned with the amount of product
•May be used to control the addition of other components to the vessel
Non-Contact vs. Non-Invasive vs. Non-Intrusive
- Non-contact implies that the device does not touch the fluid, but it could be invasive
- Non-invasive implies that the device does not pass the walls of the tank nor touch the process directly
- Non-intrusive implies that the device may come in contact with the fluid, but does not protrude into the fluid or interfere with fluid movement
Technology selection
Level Measurement Technologies
- Manual/Mechanical
- Sight glass, Gauges
- Electromechanical
- Displacer
- Electronic – Contacting
- GWR, DPT. Capacitance
- Electronic
- Non contacting Radar
- Radar, Ultrasonic
1. Continuous Level measurement
- Pressure & DP – Head type
- Displacer or Buoyancy
- Servo Displacer
- Capacitance
- Magnetostrictive
- Free Space Radar (Solids, Liquids & Custody transfer)
- Guided Wave Radar
- Ultrasonic
- Nuclear
2. Point Level measurement (Liquid)
- Ultrasonic
- Capacitance
- Vibrating – SIS
- Float/Displacer
- Nuclear
- Conductivity
- thermal
3. Point Level measurement (Solids)
•Vibrating
•Vane
•Electromechanical – YOYO
•Ultrasonic Indicators
•Sight Glass
•Armored Magnetic
Technology selection
Factors To Consider
1. Why is the level measurement needed?
What are you trying to measure?
What are you trying to achieve?
•Indication of fluid level
•Alarm set point to prevent spillover
•Transfer (Sale) of product
•Control of Product Mix
•Leak Detection
•Interface detection
2. What are the conditions within or on the vessel?
- Product turbulence/obstructions / mounting constraints
- The angle of repose for solids
- Temperature and pressure limits
3. What are the environmental conditions?
- Ambient Temperature
- Humidity
- Vibration
- Electro Magnetic Interference (EMI)
4. What are the product characteristics?
- Corrosive / Viscous/Dusty, Foam/Variable Density/
- Variable Dielectric constant/Tendency to Coat
- Interfaces, gradients, suspended solids
- Steam or other vapors
- Common Density/ Temperature Changes
- Dielectric constants
•Dielectric – A substance with a very low electrical conductivity (i.e. an insulator). Typically values < 1,000,000 mho/cm.
• The dielectric constant of a material is the ratio of the permittivity of the material under discussion to the permittivity of a vacuum. OR the amount of energy that can be stored in material or can accept an electromagnetic field compared to a vacuum.
•In level measurement terms, the dielectric constant (DK) is used to indicate the reflectivity of a material.
•Std measurements of dielectric are referenced to vacuum with a dielectric of 1. Following are DK at 20degc
Air: 1.00058
Benzene: 2.3
Acetic acid: 6.2
Ammonia: 15.5
Ethanol: 25
Glycerol: 56
Water: 81
Thumb rule:
if the material is not conductive then the dielectric value will be low; whereas conductive materials have higher dielectric values
Exception: Water
Typical Dielectric/ Temperature Changes
5. What are the instrument requirements?
- Performance requirements
- Accuracy Class – I to VI
- Location approvals
- Ex Proof / IS / Non-Hazardous
- Power requirements
- 2 Wire / 4 wire / AC 230V/110V
- Output requirements
- 4~20 mA HART / Fieldbus
- Number, location, and size of taps
- Total costs
- Product
- Installation
- Maintenance
Resources
And recently, I also found this interesting free book on Radar Level Measurement.
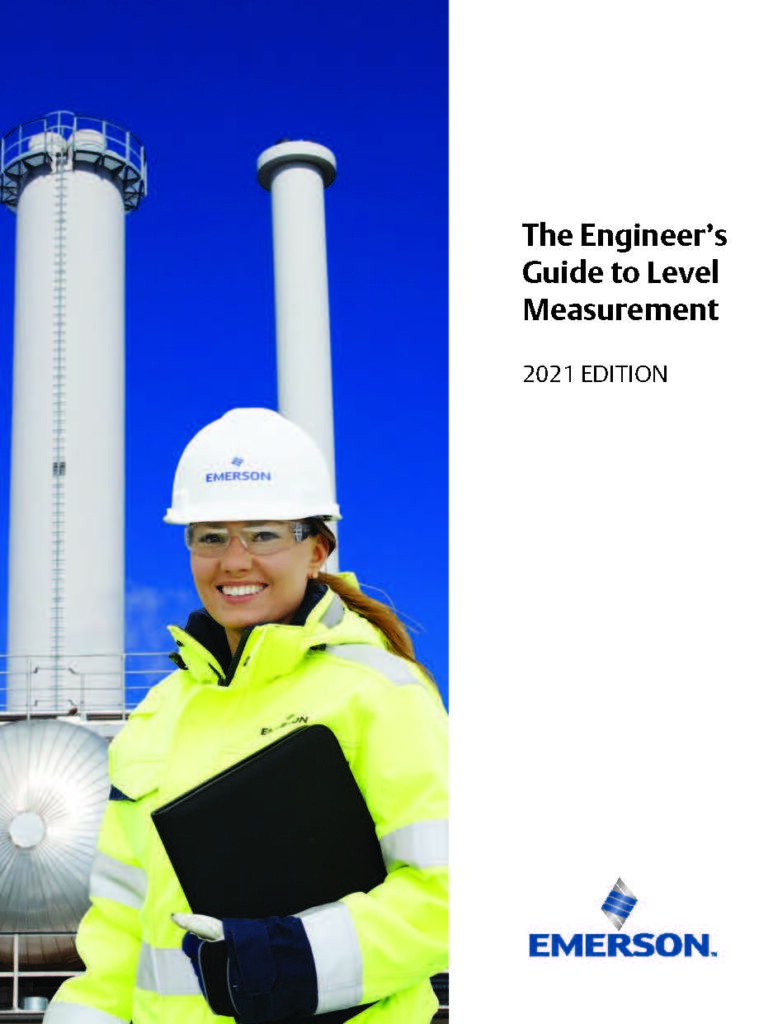
The Engineer’s Guide to Level Measurement
EndNote
I hope these resources and Knowledge will become helpful to you in the future. And I continue to make this type of resource and knowledge-sharing posts on my website.
If you have any suggestions then feel free to ask in the comments and through email id, if you want to write an article on the website, please contact us by this mail id: [email protected]
If you like this post you can also like my previous article on Ultrasonic vs Radar Level Measurement.
And you can also follow our LinkedIn group which is specially made for sharing information related to Industrial Automation and Instrumentation.