In this article, you can find a complete understanding of What is difference between PLC and DCS using Practical examples.
As you know PLC stands for Programmable Logic Controller and DCS stands for Distributed Control System.
Probably You are watching this post becomes you don’t get a proper understanding of this topic after reading many articles on the internet.
In this article, I am not focusing on the History of PLC and DCS.
Basic Overview
What is PLC?
PLC is an industrial-grade computer designed for replacing old relay logic circuits used in Industries around 1960.
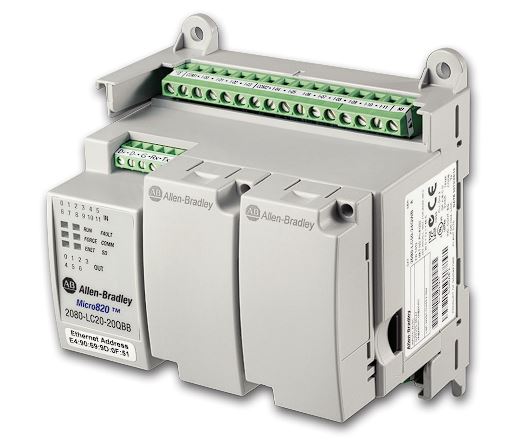
PLCs perform Logical, Arithmetical, Counter, Timer related operation very fast and efficiently and now PLCs have become modern devices that handle many tasks.
Now PLC comes with powerful Processing, communication, and diagnostic capabilities. in fact, PLCs are now used as replacements for DCS controllers. See I have not been told that PLC is used as a replacement for DCS.
But it does not mean that PLC is DCS or DCS in PLC clothing. because we are talking only about the Hardware side of DCS.
Tasks of PLC?
Process the input and provide output according to a program that is uploaded in PLC and if you want to know about PLC programming language.
then please check out my post on this topic by clicking the button given below.
Modern PLCs are capable of processing higher-level computer languages like python, c++, Matlab, and many more.
Modern PLCs have come with multiple communication protocol supports like OPC-UA, Ethernet-Based Protocol (ProfiNet, EthernetI/P, and more). and it is changed according to PLC Manufacturer.
What is DCS?
DCS is a proprietary automation turnkey solution provided by automation companies for large and complex plants.
It comes with its own custom hardware, software, and built-in framework for complete automation solutions for plants or industries.
And DCS comes with its own Custom Graphical libraries for HMI to seamlessly integrate with specific plants.
If you want to know which are the top DCS vendors in the world and their DCS systems please check out my article on this topic.
In short DCS system is a completely sophisticated solution provided by automation companies for complete automation solutions for the entire plant.
Take the Example of a Power Plant in a power plant there are many interconnected processes that are needed to control and these thousands of variables need to measure and control.
And DCS comes with customized function blocks that are used in programming that are specially made for Power Plant applications. and it changes according to industry.
And this solution has customized Hardware and Software specially designed for integration with the power plant.
PLC may be used as part of the DCS system for doing specific functions in the DCS system. Example DCS system is processing a large amount of data of the plant or process.
Due to safety reasons in critical processes safety functions are processed by a Safety instrumented system and it is one type of PLC.
Yokogawa DCS Example
YOKOGAWA’s DCS has its own SCADA function and Own controllers for doing controlling and supervision-related tasks.
It is scalable for adding more functionality to the plant according to customer needs.
YOKOGAWA’s DCS has its own tools and functionality for specific plants where DCS is mounted.
YOKOGAWA’s DCS is popular in the chemical industry. so, the DCS has come with its own pre-made tools, libraries, and function blocks for seamless integration into the Chemical application of Industry.
Why is there confusion between PLC and DCS?
- Some DCS systems are now using PLC as Hardware part and integrating with software for providing sophisticated solutions to industries.
Like ABB DCS us AC800 PLC in its DCS system
Example to distinguish Between PLC and DCS
I want to provide one funny example to create an easy understanding of this topic.
You can think of PLC as Minecraft in this it comes with a complete blank you have to build as per your own requirement.
Assume DCS as Mario Level Builder. It has a pre-maid package and functionality that you have to add to your application to full fill the requirements.
How to choose between PLC or DCS
Selecting PLC or DCS depends on multiple factors but is want to share some of them to get a general idea.
Whenever any industry chooses between PLC or DCS they need to take care of many factors.
- Complexity and Criticality of Plant
- Safety in Plant
- Number of Parameters that need to monitor and control
- Cost
- Nature of Process
- Location of Process
And there are many other parameters are needs to be considered. And it is changing according to requirements and types of industries.
EndNote: –
I hope now you have a clear understanding of what the difference is between PLC and DCS.
If and still have any doubts then please comment below I will try to resolve your doubts on this topic.