Thermocouples and RTD are the most common temperature sensors and in this post, I will show a Thermocouple vs RTD | A Complete Selection Guide.
Introduction
You probably already know about the working principles of RTD and Thermocouple. In this post, we discuss how to select between RTD and Thermocouple for Temperature measurement Applications.
What are the things that need to consider for selecting Temperature sensors for a Temperature measurement application?
And I also share what are the codes and standards that need to be followed for Selecting Thermocouple or RTD.
Basic Working Principle of RTD and Thermocouple
I already assume that you have an idea of the working principles of RTD and Thermocouple.
If you don’t have then I am sharing a summary of the basics of Thermocouple and RTD.
Thermocouple
The thermocouple is a temperature sensor that has two dissimilar metals that fussed together to create a junction point.
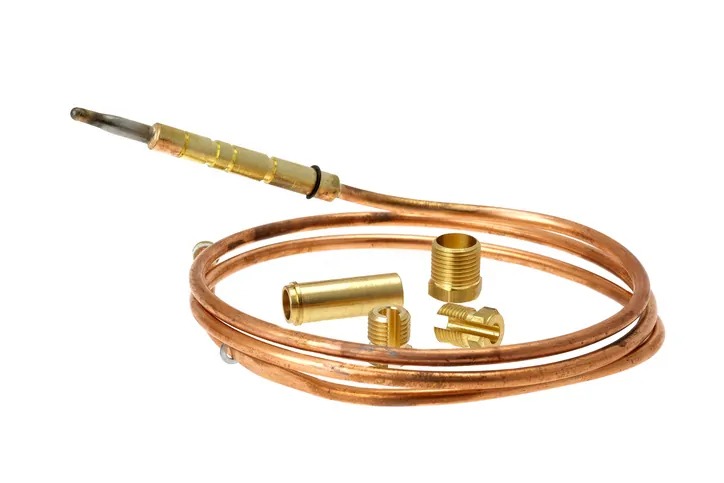
When Temperatures around the junction point are changed it will create a voltage difference at the junction point. and it is directly proportional to Temperature.
This effect of temperature to electrical conversion is called the Seebeck effect. Usually, the output of the Thermocouple is in Mv (millivolt)
There are several types of Thermocouples available in the market according to the types of Fused metal used to construct thermocouples.
For identification of the different types of thermocouples, there is a specific color code used for thermocouple cable.
form this infographic you can see the Thermocouple cable color codes as per ANSI/ISA standards.
RTD (Resistance Temperature Detector)
RTD stands for Resistance Temperance Detectors as the name suggests resistance of RTD sensor is changed according to Temperature.
Several types of RTD are used, But PT100 is the most common type of RTD that is used in the industry.
PT100 RTD comes with a Platinum-based sensing element and according to the increase in Temperature, the Resistance of this Platinum-based sensing element is also increased.
Classification of RTD
All RTDs are classified as per accuracy of output. and as per accuracy, RTD is classified into four classes as given below.
RTD class | Accuracy Range |
---|---|
AA | ±(0.1 degC + 0.17%) |
B | ±(0.15 degC + 0.2%) |
C | ±(0.3 degC + 0.5%) |
D | ±(0.6 degC + 1%) |
Specifications of Thermocouple and RTD
Specifications | Thermocouple | RTD |
---|---|---|
Range | <1200 degC | <400 degC |
Accuracy | ±1 degC | ±0.1 degC |
Cost | Cheaper than RTD | Two to Three times more costly than Thermocouple |
Sensitivity | Faster response than RTD and Grounded Thermocouple has Three times faster response than TRD | Slower than Thermocouple |
Linearity | S type plot | Linear than Thermocouple |
Stability | Output Become unstable for a long time | Output remains stable during Logn time |
Repeatability | Low | High |
Reliability | Low | High |
Codes and Standards for Thermocouple and RTD
There are different codes and standards available for thermocouples and RTD that give justifications to the specifications of RTD and Thermocouples.
Thermocouple | 1. Characteristic – IEC 584-1 2. Accuracy – ASTME-230 (1993) & ANSI MC96.1 (1988) 3. Sheath OD & Wall Thickness – ASTME-585 4.Formability – Per ASTME-585 |
RTD | IEC 751 IEC 60751 DIN 43760 ASTM E 1137 JIS C1604-1989 alpha 3916, JIS C 1604-1997 SAMA RC21-4-1966 GOCT 6651-84, GOST 6651-94 Minco Table 16-9 Edison curve #7 |
How to select Thermocouple or RTD for Temperature Measurement Application
I will give you a step-by-step guide for selecting the right temperature measurement sensor for your application.
Step 1: Temperature Range
The first criteria for selecting between a Thermocouple or RTD is the Range of temperature that needs to be measured.
For the above 400 degC application, we have only one option and it is Thermocouple.
Step 2: Response Rate
If the temperature range is below 400 degC then we have to look at the response of process criticality of the process.
If the temperature changes quickly then we have to choose a thermocouple to become the response rate thermocouple is high.
Step 3: Accuracy and Repeatability
After the Temperature range and Response rate now, we have to focus on the reliability of our sensors.
If the application requires highly reliable sensors that produce highly accurate output repetitively then we have to choose RTD.
Step 4: Linearity and Stability
If the application requires linear and stable output for a long period or you can say less maintenance is required.
for less maintenance, we have to choose RTD because the output of RTD is linear and stable in the long run.
Step 5: Cost
For small applications, the cost factor also affects the selection between RTD and Thermocouple.
The thermocouple is Cheaper than RTD. if You notice that I discuss the cost factor at the end becomes other parameters are very important than cost.
EndNote: –
I hope now you have a clear understanding of how to select between Thermocouple or RTD.
Now you also have an idea about different standards and codes for RTD and Thermocouple sensors.
You can also check out my latest post on the Standard and Specification of the control valve that needs to be followed for selecting the control valve.