Introduction: –
Many of you are confused about what is the difference between PLC, SCADA, and DCS. By using my Engineering knowledge, I will resolve all your confusion on PLC/SCADA and DCS.
Some of the articles on the internet make you more confused on this topic. And the articles had been written using hard language so you can’t reach a proper conclusion. In short, articles on this topic are not Straight to the point.
I will not give you only a theoretical explanation but also, I will be trying to resolve your doubts based on a practical approach.
I hope after reading this post you will easily distinguish between PLC vs SCADA vs DCS.
Types of industries: –
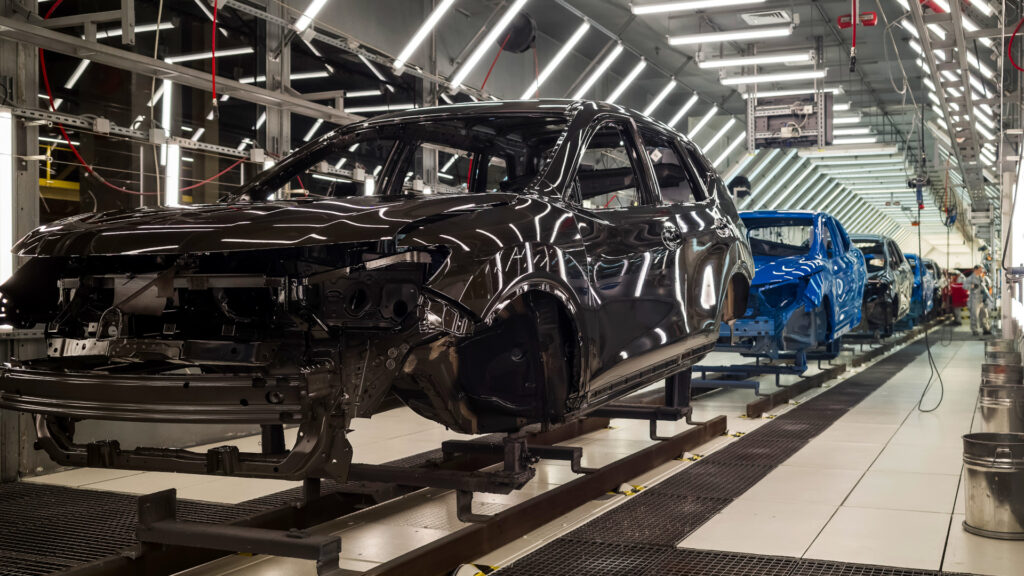
Mainly industries are divided into three parts according to their working principles. and these three types are given below.
- Discrete type
- Continuous type
- Hybrid type
Discrete process Industries: –
In Discrete type process industries, the Process is not continuous (Obviously) and one process in not depend on the other process. like the Automotive industry.
Continuous process industry: –
In continuous-type process industries, an operation is continuously running and one parameter of the industry will depend on other parameters. Like Oil and Gas, Chemicals, Power
Hybrid process Industry: –
in hybrid-type industries some other processes are continuous and some processes are discrete so this type of operation is called hybrid operation. Like life science.
What is PLC?
PLC (Programmable Logic Controller) is an industrial-grade computer that is used for processing field parameters according to logic stored in PLC memory.
PLC consists of an IO card for interfacing field input and output. More about PLC will be posted on this site so stay tuned.
PLC is the replacement of the old relay logic control. Replacing PLC instead of a Relay logic circuit helped the industry to reduce installation and maintenance costs and also reduce complexity.
What is SCADA?
SCADA (Supervisory Control and Data Acquisition) is pics of software that is specially made for the supervision of multiple PLCs and RTUs.
When the process becomes complex and decentralized (Multiple processes take place in multiple locations) multiple PLCs and RTUs are used for distributing tasks.
The Main Function of SCADA displays Data and Alarms through HMI. For Example, Ignition is SCADA software provided by Inductive Automation and you can see software is deployed on the server.
Communication between PLC and SCADA software is happening through different communication protocols like OPC-UA and MQTT.
SCADA software is vendor-independent. SCADA software easily communicates with multiple vendors PLCs and RTUs.
What is DCS?
DCS is a proprietary automation solution provided by automation companies for large and complex plants. DCS has its custom hardware and software solution for controlling and monitoring related takes.
Nowadays DCS supports open communication standards like Profibus, ProfiNet, HART, etc. for integrating products from multiple vendors.
For Example, YOKOGAWA’s DCS has its SCADA function and Own controllers for doing controlling and supervision-related tasks and it is scalable for adding more functionality in a plant according to customer needs.
YOKOGAWA’s DCS has its tools and functionality for specific plants where DCS is mounted.
Like YOKOGAWA’s DCS is mostly used in chemical plants so the DCS has come with its tools and libraries for seamless integration to the customer’s site.
How to choose between PLC SCADA or DCS
For choosing between PLC SCADA or DCS. We have to learn about the scale of automation and also have to consider the complexity and criticality of the process.
Scales of industrial automation: –
- Small-scale automation
- Medium-scale automation
- Large-scale automation.
1. Small scale Automation: –
In small-scale automation, a smaller number of Input and Output signals are needed. In small-scale automation, all the companies follow a centralized approach and are selected to use PLC for the application.
Because of the less complexity of small-scale automation, there is no need to implement these listed functions.
- Alarm management
- Redundancy
- Plant historian
- Plant report generation
- High-speed communication network
Usually, PLC is selected for small-scale automation in the industry. discrete machine automation is done by PLC
PLC has fast resources so it is used in ESD (Emergency Shutdown System) or SIS (Safety Instrument System) system in Plants where DCS is used and this PLC will directly communicate with DCS.
Examples of industries with small-scale automation: –
- Small Packaging industries
- CNC machines
- Small metal cutting industry
- Injection modeling machine
2. Medium-scale automation
In medium-scale automation, multiple processes are distributed across the plant, and for controlling individual processes separate PLCs are used. Because of multiple PLCs, there are many Processes I/O needs to monitor and control.
SCADA software is selected for monitoring and controlling plant parameters through the HMI. These are all the features available in SCADA software.
- HMI building
- Alarm configuration and management
- Report generator
- Real-time monitoring
- Industrial Historian
If you are interested in knowing about SCADA software provider companies then check out my post: – what are SCADA and SCADA software Provider companies?
Examples of industries that use SCADA: –
- Automobile 🚗 Manufacturer companies: – Toyota, Suzuki, Honda, Hero, etc.
- Food processing industries: – Balaji, ITC, Nestle
- Dairy Industries
3. Large scale automation
In large-scale automation, there are multiple processes spread across the plant and some of the processes are critical. for controlling the large-scale plant SCADA or DCS is used.
When plant safety becomes a priority then the DCS system is preferred because the DCS system is running in fully redundant mode. If one piece of equipment fails the other one is taken over.
Big automation companies come with their proprietary DCS system for entire plant automation and also consider safety as well. SPPA-T300 is a DCS solution provided by Siemens specifically for power plants.
And this DCS system has integrated SCADA functionality for data gathering and monitoring and a specialized controller is used for controlling purposes.
Examples of industries using DCS control systems: –
- Oil and Gas Refinery
- Power plant
- Water Treatment Plant
- Cement making industries
- Some Chemical Plants
Difference Between PLC/SCADA and DCS?
Ideally, there is no comparison between PLC/SCADA and DCS. PLC/SCADA and DCS come with their specifications and advantages. But for your understanding, I was provided information in a comparison format.
PLC | SCADA | DCS |
---|---|---|
The full form of PLC is “Programmable Logic Controller” | The full form of SCADA is “Supervisory Control and DATA Acquisition” | The full form of DCS is “Distributed Control System” |
A centralized controller is used for automation tasks | A basic communication structure is used | Dedicated solution providing for large and complex process industries. |
Software used for programming provided by Manufacturer companies | Multiple software vendors are available in the market. | Software is provided only by DCS Vendors company |
Redundancy is possible | Redundancy is possible | Redundancy is possible at every level |
Downtime is only converging into loss of production | Downtime is converging into loss of production, equipment failure, and creating hazardous situations | Downtime is very crucial because massive dangerous situations will be created and converge into losses of money and lives |
Basic control strategies are implemented | Complex control strategies are implemented | Complex and more advanced control strategies are implemented |
Basic communication structure is used | Advance and foster communication structures are used | Advance and complex communication is used with high-speed communication. |
Implications const is low compared to other | Implementation cost is higher than PLC but lower than DCS | The cost of DCS implementation is the highest |
PLC provider companies: – Siemens, ABB, Allan Bradley, Schneider | SCADA software provider companies: – Inductive Automation, Rockwell Automation, Siemens, Aveva | DCS providers companies: – Yokogawa, ABB, Emerson, Rockwell Automation, Schneider |
EndNote: –
In this post, I will give you a general overview of PLC/SCADA and DCS. PLC/SCADA and DCS are individual deep-learning topics for automation.
After watching this post, you will be able to find differences between PLC/SCADA and DCS. If you have any questions then comment below.
Thank you Kishan – a basic and understandable treatment of the subject. Just two comments from my side :-
a – you imply the use of DCS in processes where there are safety related concerns. I would say the days when we used DSC (or PLC for that matter) in safety applications have long since passed. You should introduce the concept of Safety Instrumented System as distinct from DCS in this regard
b – there is one DCS that you should look at in more detail – ABB’s Freelance. This is a full featured DCS platform but can also be run in their AC700F controller which is hardware wise the same hardware as their AC500 PLC as you show above. Freelance is perhaps one the the finest products in the world as a pure DCS but with the AC700F they have a very impressive “DCS in PLC clothing” …………..
Best Regards
Paul
I will give a detailed answer to my upcoming article
Thank you for your reply