Having a proper idea about the 4-20mA Current loop helps you in industrial instrument maintenance tasks and troubleshooting of problems.
Introduction
There are many electrical and other analog signals used in industry to transmit analog values from controller to field instruments or instruments to the controller.
- 1 to 5V
- 4 to 20mA
- 3 to 15 psi
- 10 to 50mA
- 0 to 20mA
- 0 to 5 VDC
- -10 to 10 VDC
The most commonly asked question is why for analog signal transmission only 4-20mA signal is considered Not any other like 3-16mA, 20-45mA, 0-50mA Etc.
We also have doubts that why we do not use voltage signals instead of the current signal. Ultimately PLC is reading voltage signals.
Because in the end, we have to convert the current signal into a voltage signal using precision Resistors.
Why Only 4-20mA Current loop?
There are multiple responses for selecting 4-20mA Current loop as a standard for industrial parameters. Before this, I want to define some terms for further explanation.
In the 4-20mA signal, I want to define the 4mA signal as Lower End Valve and 20mA Signal is considered as upped end value.
Why 4mA is the Lower end Value?
Reason 1 | Loop Power
We can’t consider 0mA as a lower-end value because it does not work for the two-wire transmitter (Loop powered). Two wire transmitters get their power from a loop.
If there is no current flowing in the loop (0 mA), then there is no power for the instrument to keep its circuitry active.
In order to use an instrument on a loop that has 0 mA or 0 VDC as the low end, it only works for 3-wire or 4-wire instruments becomes it is connected to a separate power supply source.
Reason 2 | 20% of Upper-End Valve
When you look at the above-listed widely used standard signals you can find one pattern that appears that relates the upper-end value and lower-end value of the signal.
You can see that the lower-end value is exactly 20% of the upper-end value and now you can guess that 4mA is 20% of 20mA you can also see in 3-15 Psi, 1-5VDC.
Reason 3 | Live Zero
This is the common answer you can find on the internet that why 4-20mA signal is used in industries.
One important reason is live zero measurements, which means that when the controller reads a 0 value you will distinguish that the Measuring parameter is not zero but either there is a wiring fault or transmitter fault.
Why 20mA is the Upper-end Value?
20 mA communications have been around since the first half of the 20th century in the form of teletype machines (such as the ASR33, by Teletype Corporation, and the 32-ASR by Telex).
Technical people were accustomed to dealing with 20 mA components in the digital applications of teletype machines, so it may have had some bearing on choosing 20 mA as the high limit of the 4 to 20 mA loop, rather than some other value like 30 mA.
Benefits of 4-20mA signal
- Offer intrinsic safety because it has low energy compared to 10-50mA that’s why 4-20mA is chosen over 10-50mA.
- Easily converted to 1-5VDC signal using 250Ohm Resistor. By using the ohm law you can that by connecting a 250ohm Resistor in series you can get 1-5VDC across the resistor that can be directly read by the Controller.
But connected 250Ohm Resistor should be a precision (0.01% or better) resistor to convert the 4-20mA signal to 1-5VDC Accurately.
Some signal conditioners or isolation modules use a 100-ohm (or smaller) resistor to convert the 4 to 20 mA signal to a 0.4 to 2 V Signal. Converter resistor will change as per Controller Manufacturer.
The voltage of the Power supply in the two-wire transmitter is selected according to Maximum loop resistance.
Maximum Loop Resistance = Power Supply voltage / 20mA
If the loop resistance is higher than the Calculated Maximum Loop Resistance then we have to increase the supply voltage.
References
- ISA publication ANSI/ISA-50.00.01-1975 (R2002) Compatibility of Analog Signals for Electronic Industrial Process Instruments.
Resources
And recently, I also found this interesting free book on Understanding 4-20mA Current Loop.
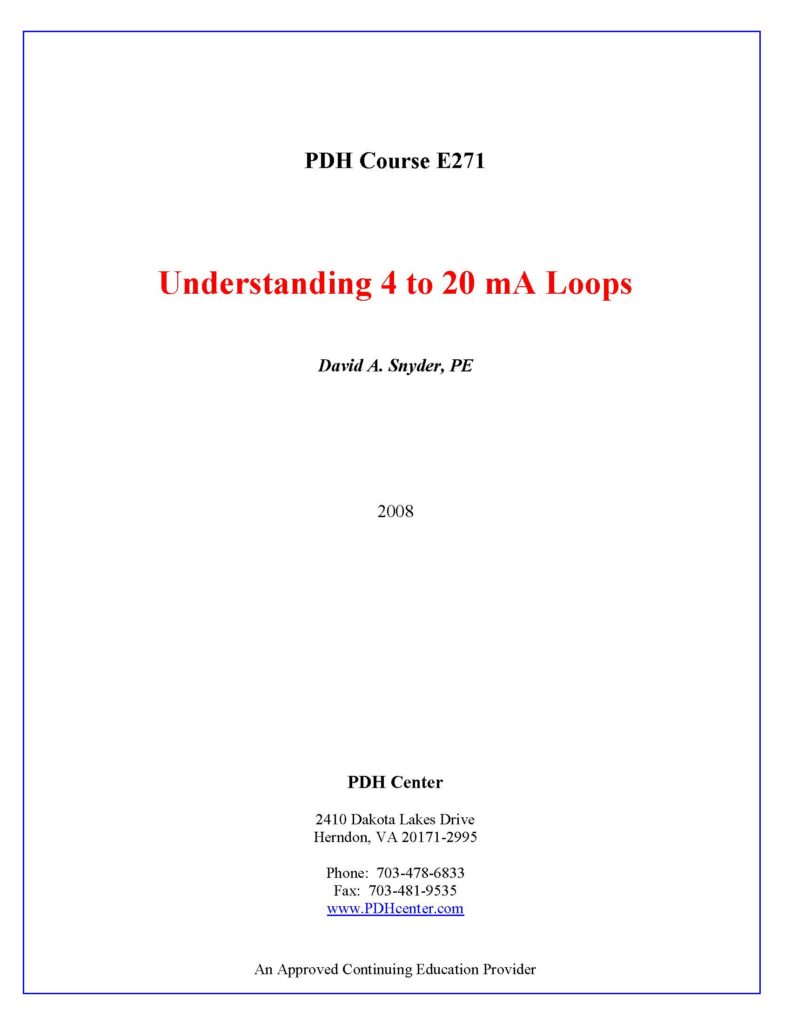
Understanding 4-20mA Loop
EndNote
I hope these resources and Knowledge will become helpful to you in the future. And I continue to make this type of resource and knowledge-sharing posts on my website.
If you have any suggestions then feel free to ask in the comments and through email id, if you want to write an article on the website, please contact us by this mail id: contact@worldofinstrumentation.com
If you like this article, you can also like my previous article on the Factory Acceptance Test (FAT) Procedure of PLC/DCS
And you can also follow our LinkedIn group which is specially made for sharing information related to Industrial Automation and Instrumentation.